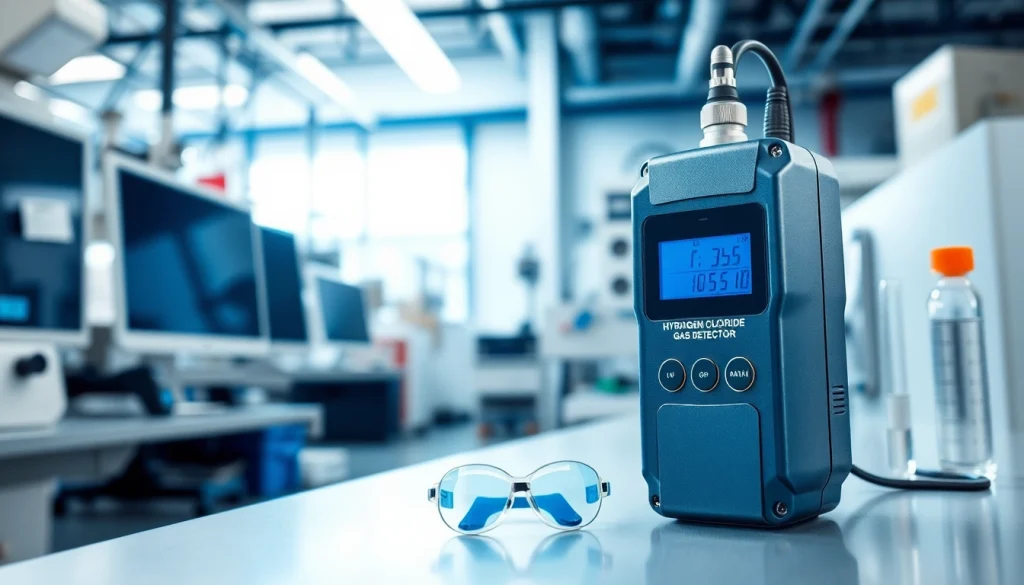
What is a Hydrogen Chloride Gas Detector?
Definition and Importance
A Hydrogen Chloride gas detector is a device designed to sense the presence of hydrogen chloride (HCl) gas in the environment. This gas, known for its pungent odor and corrosive properties, can pose serious risks to health and the environment when levels exceed permissible limits. HCl is commonly utilized in industrial processes including chemical manufacturing, metal processing, and oil refining, making the detection of this gas critical for workplace safety and compliance with environmental regulations. Given its potential to cause respiratory irritation and damage to the lungs and mucous membranes, having an efficient Hydrogen Chloride gas detector becomes essential in industries where exposure might occur.
How They Work
Hydrogen Chloride gas detectors operate on various technologies including electrochemical sensors, infrared sensors, and photoionization detectors (PID). Each technology has its strengths and is chosen based on the application requirements. For instance, electrochemical sensors are highly sensitive and widely used for personal safety monitoring. When HCl comes into contact with the sensor, a chemical reaction generates a current proportional to the gas concentration, which the device measures and displays. Infrared sensors detect gas concentration by analyzing the absorption of infrared light specific to HCl molecules. PIDs, on the other hand, utilize ultraviolet light to ionize gas molecules, making them suitable for detecting low concentrations of HCl.
Types of Detectors Available
There are various types of hydrogen chloride gas detectors available, tailored to specific applications and environments:
- Fixed Gas Detectors: Permanently installed systems that continuously monitor HCl levels in a designated area, often used in industrial settings.
- Portable Gas Detectors: Handheld devices designed for personal monitoring and spot checks in various locations, making them ideal for maintenance and emergency responders.
- Remote Monitoring Systems: Advanced systems featuring wireless capabilities to transmit data to central monitoring locations, enhancing safety by enabling real-time analysis and response.
Key Features of Hydrogen Chloride Gas Detectors
Detection Range and Sensitivity
The efficacy of a hydrogen chloride gas detector significantly hinges on its detection range and sensitivity. Detectors are designed to pick up HCl concentrations typically measured in parts per million (PPM). For reliable operation in environments where HCl is present, detectors should have a low detection threshold, capable of identifying concentrations far below harmful levels. Some advanced models feature adjustable sensitivities, allowing users to modify detection ranges based on specific operational needs. This flexibility is crucial in preventing false alarms while ensuring safety during multi-gas monitoring.
Calibration and Maintenance
Regular calibration is vital for maintaining the accuracy and reliability of hydrogen chloride gas detectors. Calibration involves comparing the detector’s readings with known standard concentrations of HCl, adjusting for correctness as necessary. Most manufacturers recommend calibration at least once a year; however, frequent exposure to high concentrations or harsh environments may necessitate more regular checks. Additionally, routine maintenance practices such as cleaning sensor surfaces, verifying battery life, and conducting functional tests should be implemented to minimize downtime and maximize detector performance.
Data Logging Capabilities
Modern hydrogen chloride gas detectors often come equipped with data logging features, enabling users to track exposure levels over time. Data logging can facilitate compliance with occupational safety regulations and support accident investigations by providing historical concentration data. High-end models allow for extensive data capture, offering users the ability to generate detailed reports, analyze trends, and store data securely for future reference. The integration of data logging capabilities into a hydrogen chloride gas detection system can empower organizations to improve safety protocols and ensure regulatory compliance.
Applications in Various Industries
Chemical Manufacturing
In the chemical manufacturing sector, hydrogen chloride is widely used in the production of various chemicals. As exposure risks are inherent during processes such as synthesis and transportation, using reliable gas detection technologies is paramount. Facilities often install fixed gas detectors in areas where hydrogen chloride is produced, stored, or used. Moreover, portable detectors serve as essential tools for workers involved in maintenance tasks, allowing them to assess safety conditions before commencing work.
Environmental Monitoring
Hydrogen chloride gas detectors play a crucial role in environmental monitoring, especially in areas near industrial activities where HCl emissions may occur. Regulatory bodies require continuous air quality assessments to protect the public and the environment from harmful pollutants. Implementing both fixed and portable detectors can ensure that local air quality is within permissible limits. Data collected from hydrogen chloride monitoring can also serve as essential information for decision-making processes in municipal planning and environmental impact assessments.
Safety and Compliance Regulations
The use of hydrogen chloride gas detectors is often mandated by safety and compliance regulations across various industrial sectors. Organizations must adhere to guidelines set by regulatory bodies such as OSHA (Occupational Safety and Health Administration) and EPA (Environmental Protection Agency). Compliance includes the implementation of gas detection systems to safeguard against overexposure and the establishment of safety protocols for emergency situations. Failure to comply can result in substantial fines and, more importantly, jeopardize worker safety and health.
Choosing the Right Hydrogen Chloride Gas Detector
Assessing Your Needs
When selecting a hydrogen chloride gas detector, organizations must first assess their unique operational needs. Considerations should include the expected concentration levels of HCl, the environment (indoors or outdoors), and whether the application necessitates fixed or portable detection systems. Additionally, think about monitoring frequency and specific safety regulations applicable to the industry. Gathering input from occupational safety experts and involving personnel who will be using the detectors can provide valuable insights into the selection process.
Budget Considerations
Budget constraints will invariably influence the type of hydrogen chloride gas detector a facility can afford. While top-of-the-line models with advanced features may offer superior detection capabilities and data logging functions, cost-effective alternatives might suffice for less demanding applications. Organizations should weigh initial purchasing costs against long-term operational advantages, such as reliability, maintenance needs, and longevity, to ascertain the best fit for their financial and safety requirements.
Top Brands and Models
Several manufacturers stand out in the hydrogen chloride gas detection market, offering models that cater to diverse industrial applications. Brands like Dräger, Honeywell, and MSA Safety provide well-regarded options known for reliability and performance. Models such as the Dräger X-am 2500 or the Honeywell BW Gas Alert provide a combination of portability and functionality to meet varying detection needs. Organizations should research product reviews, consult with manufacturers, and analyze specifications to identify the best models available in their industry.
Best Practices for Maintaining Hydrogen Chloride Gas Detectors
Regular Calibration Procedures
Establishing a routine calibration schedule is one of the most important tasks for ensuring the accuracy of hydrogen chloride gas detectors. Organizations should implement a preventive maintenance strategy that includes the standardized calibration of all detectors at recommended intervals, typically following the manufacturer’s guidelines. Documentation of all calibration activities, including outcomes, repairs, and adjustments, should be maintained to ensure regulatory compliance and performance tracking.
Common Issues and Troubleshooting
Some common issues encountered with hydrogen chloride gas detectors include false alarms, incorrect readings, and sensor failure. False alarms can often be attributed to interference from other gases or environmental conditions; thus, understanding the detector’s limitations and environmental implications is essential. When troubleshooting, users should first check sensor responsiveness by exposing it to known concentrations of HCl. Receiving technical support directly from manufacturers can provide further guidance on resolving persistent issues effectively.
Staying Compliant with Safety Standards
To avoid legal ramifications and safeguard employees, organizations must stay informed regarding safety standards and regulations related to hydrogen chloride detection. Regular audits of gas detection systems, ongoing training for employees on recognizing safety protocols, and participation in safety drills enhancing response capabilities are vital elements in maintaining compliance. Engaging with industry experts to stay updated on regulatory changes and technological advancements is equally essential in ensuring detection systems meet or exceed compliance requirements.