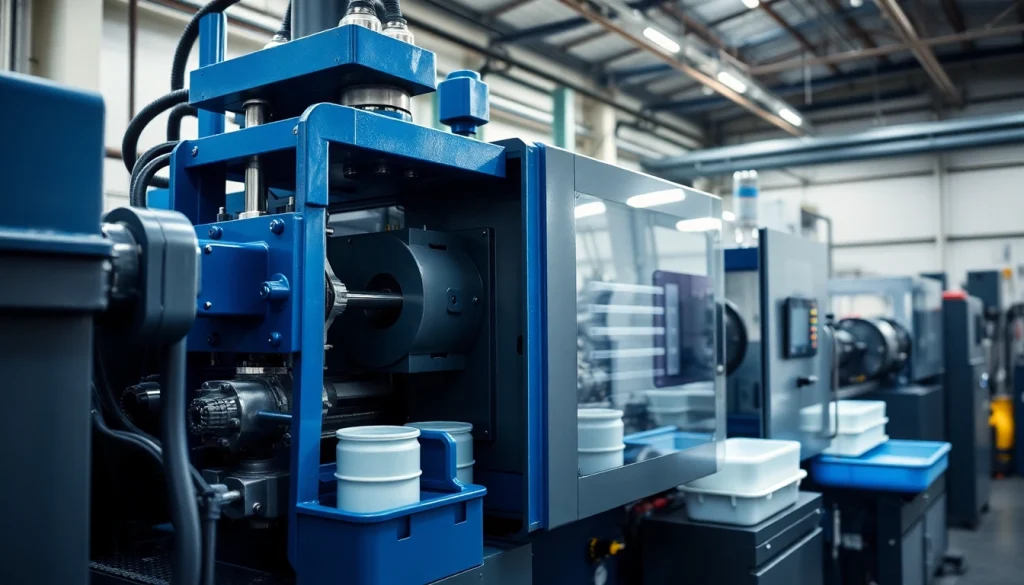
Introduction to Blow Molding Technology
Blow molding is a pivotal process in manufacturing hollow plastic objects. It enables the mass production of containers, bottles, and various other shapes that serve a multitude of industries, from consumer goods to pharmaceuticals. As a leading Blow Molding Machine Manufacturer, it is imperative to understand the intricacies of this technology to enhance production efficiency and maintain quality in output.
What is Blow Molding?
Blow molding is a manufacturing process that involves inflating a hot, hollow plastic tube (known as a parison) into the shape of a mold. This technique is essential for producing not just bottles, but a wide variety of products including automotive parts, toys, and medical devices. The process can be defined in three main categories: extrusion blow molding, injection blow molding, and stretch blow molding—all of which cater to different requirements and specifications in product design and economics.
Applications of Blow Molding Processes
This process is widely applied across various industries:
- Packaging: Most commonly, blow molding is used to make plastic bottles and containers. With the increasing demand for lightweight and durable packaging, companies utilize blow-molded containers as they offer strength and design flexibility.
- Automotive: Utilized for producing hollow parts like fuel tanks and interior components, blow molding can significantly reduce weight, thereby enhancing fuel efficiency.
- Consumer goods: Products such as toys and household containers often leverage blow molding technology to meet quality and durability requirements.
- Medical: Specific applications involve manufacturing medical device casings, which require stringent hygiene and precision standards.
Overview of Different Types of Blow Molding
Understanding the different blow molding processes can help manufacturers choose the right approach based on their specific production needs:
- Extrusion Blow Molding (EBM): In EBM, a continuous plastic tube is extruded and formed into a mold. This process is ideal for larger parts like tanks and containers. The benefits include relative simplicity and low-cost mold construction.
- Injection Blow Molding (IBM): This method combines both injection and blow molding processes. It is particularly suitable for creating high-precision parts and finishes, aimed at producing smaller, complex items such as cosmetic bottles and pharmaceutical containers.
- Stretch Blow Molding (SBM): Predominantly used for making bottles from pre-formed PET preforms, this method offers excellent strength and is highly efficient for high-volume production.
Choosing the Right Blow Molding Machine
Selecting the appropriate blow molding machine is integral to optimizing production efficiency and profitability. Factors that come into play include production volume, product specifications, and material compatibility.
Key Factors to Consider
When evaluating blow molding machines, several key factors must be considered:
- Production Capacity: Understanding your anticipated production volume will guide you in selecting a machine that can handle your needs without excessive downtime.
- Material Compatibility: Not all machines accommodate every type of plastic. Ensure that the machine you choose is compatible with your preferred materials.
- Cost and Budget: Evaluate total cost of ownership, including the initial purchase price, maintenance costs, and availability of parts and service.
- Technology Type: Depending on your application’s requirements, certain technologies (EBM, IBM, SBM) may be more suitable than others. Assess your production goals and product designs.
Comparing Injection vs. Extrusion Blow Molding
A critical decision looms between choosing injection and extrusion blow molding. Each method has its pros and cons:
- Injection Blow Molding: Provides high precision and thickness control, ideal for smaller, complex shapes but often entails higher tool costs.
- Extrusion Blow Molding: Simpler and more cost-effective for larger products, but may sacrifice some detail and precision typically desired in smaller items.
Understanding Machine Specifications
Each machine will have specifications that determine its capability. Key specifications include:
- Clamping Force: This is crucial as it will determine how much pressure the mold can withstand.
- Shot Size: Indicates the volume of material that can be injected, which impacts the size of the products produced.
- Cycle Time: Shorter cycle times can significantly enhance production rates.
Industry Trends and Innovations
The blow molding industry is experiencing rapid evolution with various trends and innovations shaping its future.
Emerging Technologies in Blow Molding
Innovation is a continuous theme in manufacturing. Some of the notable advancements include:
- 3D Printing: Companies are beginning to use 3D printing to create prototypes for blow molds, reducing development times significantly.
- Smart Manufacturing: The rise of sensors in machinery allows real-time data monitoring, improving predictive maintenance, and reducing downtime.
- Advanced Materials: The development of lightweight and high-strength materials allows for the production of even more sophisticated components.
Impact of Industry 4.0 on Manufacturing
Industry 4.0 significantly reshapes manufacturing, enhancing automation and connectivity. Implementing IoT devices within blow molding operations allows for:
- Improved Efficiency: Real-time monitoring enhances workflow management, minimizes waste, and reduces energy consumption.
- Data Analytics: Gathering insights through data analytics helps in decision-making and strategic planning.
- Customization: Automated systems allow for quick adjustments to production, enabling greater customization options for clients.
Sustainability Practices in Blow Molding
As sustainability becomes a priority, manufacturers are focusing on eco-friendly practices:
- Recyclable Materials: Using high-quality recyclable plastics supports both the environment and meets consumer demand.
- Energy Efficiency: Investing in energy-efficient equipment and processes reduces the carbon footprint of production.
- Waste Reduction: Leveraging technologies to reduce scrap and by-products during the molding process minimizes waste significantly.
Identifying Top Blow Molding Manufacturers
Finding a reliable blow molding manufacturer involves assessing various aspects that contribute to their reputation and service quality.
Evaluating Company Reputation and Experience
Reputation is built over years of consistent quality. Assess potential manufacturers by:
- Industry Experience: Companies with a long-standing history in the industry are likely to have refined their manufacturing processes successfully.
- Global Reach: Manufacturers with a global presence often indicate robust processes and quality assurance standards.
Customer Reviews and Case Studies
Customer feedback is invaluable in the decision-making process. Look for:
- Testimonials: Genuine reviews provide insights into customer satisfaction and product performance.
- Case Studies: Evaluate case studies highlighting past projects, which can showcase a manufacturer’s strengths and successful implementations.
Price Range and Product Offerings
Budgetary constraints significantly influence purchasing decisions. When assessing price ranges, consider:
- Total Cost of Ownership: Beyond initial pricing, include maintenance and operational costs in your evaluation.
- Customization Options: Ensure the manufacturer is willing to work with you to customize machines that meet specific production requirements without exorbitant costs.
Maximizing Production Efficiency
Efficiency is essential in manufacturing processes. Here are actionable strategies to ensure optimal production in blow molding:
Best Practices for Operation and Maintenance
Effective operation and maintenance practices can prolong machine life while ensuring top performance:
- Regular Inspections: Conduct frequent inspections to identify potential issues early, which can prevent significant breakdowns.
- Scheduled Maintenance: Adhering to a strict maintenance schedule significantly reduces the likelihood of unexpected downtime.
- Employee Training: Ensuring that operators are well-trained can prevent user error, which is a common cause of operational inefficiencies.
Reducing Downtime and Increasing Output
Minimizing downtime is key to maximizing productivity. Strategies include:
- Predictive Maintenance: Utilize data analytics to anticipate when maintenance is required, avoiding unplanned outages.
- Process Standardization: Developing standard operating procedures can help maintain consistency and streamline transitions between production runs.
- Inventory Management: Efficient inventory practices ensure that materials are always on hand, thus avoiding production stoppages.
Addressing Common Challenges in Blow Molding
Manufacturers face numerous challenges, including:
- Material Defects: Overcoming material quality issues can involve stringent supplier vetting processes and thorough quality control methodologies.
- Complex Molding Geometries: Innovative tooling design, like using simulation software, can aid in the successful production of complex shapes.
- Market Fluctuations: Keeping abreast of market changes will allow manufacturers to be agile, adapting their production and innovation strategies accordingly.