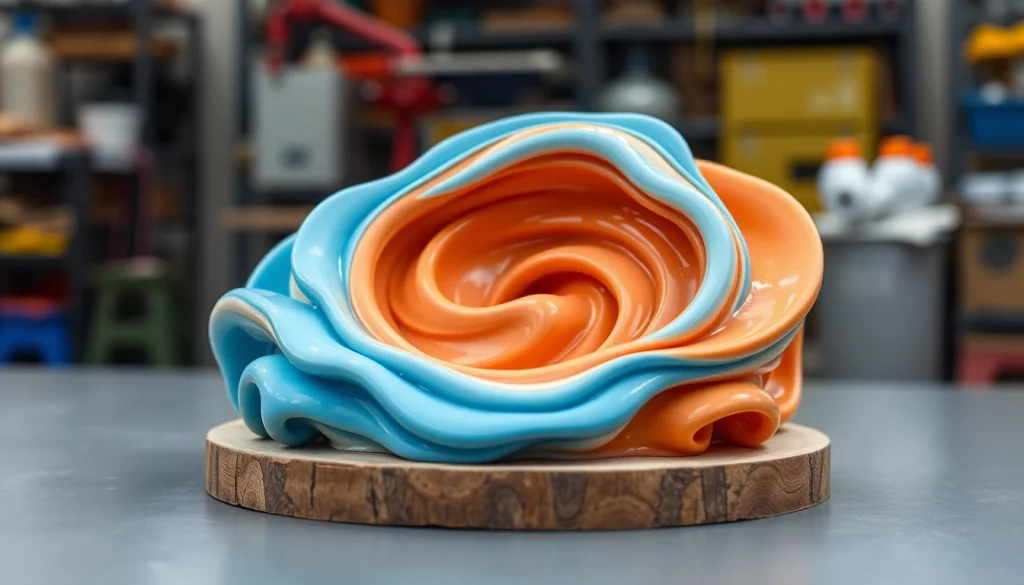
Understanding Blow Molding Technology
What is Blow Molding?
Blow molding is a manufacturing process that involves inflating soft plastic into a mold to create hollow objects. It is primarily used in producing large quantities of plastic parts, particularly packaging items like bottles and containers. The process employs the principles of thermodynamics to manipulate the plastic’s malleability under heat and pressure, turning solid resin into a pliable form before shaping it within molds. This method is favored for its efficiency in producing uniform and complex shapes at reduced costs, making it a standard choice for many industries.
Types of Blow Molding Processes
There are three main types of blow molding processes:
- Extrusion Blow Molding (EBM): In this process, plastic is melted and extruded into a parison. The parison is then inflated within a mold to form the desired shape. EBM is commonly used for producing bottles and hollow containers in high volume.
- Injection Blow Molding (IBM): This method combines injection molding and blow molding. A preform is created using injection molding, which is then inflated to shape in a second process. IBM is typically used for creating round bottles with precise designs.
- Stretch Blow Molding (SBM): This process involves stretching the parison in both axial and radial directions, leading to thinner walls and better strength. SBM is ideal for producing lightweight bottles that require a high degree of transparency.
Applications of Blow Molding
Blow molding is utilized across various industries due to its versatility. Common applications include:
- Bottles: The beverage industry heavily relies on blow molding to create plastic bottles for soft drinks, water, and other liquids.
- Containers: Many food and personal care products are packaged in blow-molded containers, ensuring they are lightweight yet durable.
- Tanks and Large Housings: Blow molding is also used for creating larger items like chemical tanks and auto parts that require durable plastic materials.
Choosing the Right Blow Molding Machine
Key Features to Consider
Selecting the appropriate blow molding machine is critical for optimizing production efficiency and product quality. Important features to evaluate include:
- Machine Type: Determine if the intended products are better suited for extrusion, injection, or stretch blow molding based on the desired output.
- Production Capacity: Assess the machine’s throughput and its capability to meet production demands while maintaining quality.
- Automation Features: Consider machines with advanced automation capabilities for improved efficiency, reduced labor costs, and decreased chances of error.
- Energy Efficiency: Look for machines that utilize technologies aimed at reducing energy consumption, as this can significantly impact operating costs.
- Maintenance Ease: Evaluate features that simplify maintenance, such as easy access to parts and automated diagnostic systems for troubleshooting.
Evaluating Manufacturer Options
The choice of a blow molding machine manufacturer can greatly influence the overall success and efficiency of your production operations. Here are several factors to consider:
- Reputation: Research the manufacturer’s standing in the industry, looking for feedback from other users regarding reliability and service.
- Support and Service: Investigate the availability of after-sales support, including training, spare parts, and technical assistance when needed.
- Customization: Some manufacturers offer tailored solutions, allowing you to modify machines based on specific production requirements.
- Industry Expertise: Choose manufacturers with experience in your industry, as they will better understand the challenges and requirements you face.
Cost Factors in Blow Molding Machines
Understanding the cost implications associated with blow molding machines is essential in making an informed decision:
- Initial Investment: Evaluate the total cost, including the price of the machine, installation, and any necessary accessories or modifications.
- Operating Costs: Estimate energy consumption, labor, maintenance, and any material costs associated with running the machinery over time.
- Return on Investment (ROI): Calculate potential savings on labor, material waste reduction, and increased production speeds to determine the long-term benefits of the investment.
Top Blow Molding Manufacturers in the Industry
Analyzing Leading Competitors
The market for blow molding is competitive, with several key players recognized for their innovative technologies and reliable machines. Some notable companies include:
- Uniloy: A global leader that offers a range of blow molding technologies, including innovative solutions tailored for various market needs.
- Wilmington Machinery: Renowned for high-speed monolayer and multilayer rotary extrusion blow molding machines, it caters to diverse production needs.
- Jomar Corporation: Celebrated for its expertise in injection blow molding machines, Jomar has established a strong foothold in the industry over the past five decades.
- Bekum Maschinenfabrik GmbH: Known for its successful H-series blow molding machines, Bekum continues to deliver reliable solutions in North America.
- Graham Engineering: Offers a variety of blow molding solutions, including innovative systems designed for high efficiency and quality consistency.
Market Trends and Innovations
The blow molding industry continues to evolve, driven by technological advancements and changing market demands. Key trends include:
- Industry 4.0: The adoption of smart technology and IoT in blow molding machines is optimizing operational efficiency and predictive maintenance.
- Sustainability: Increasing consumer demand for sustainable products is prompting manufacturers to explore eco-friendly materials and energy-efficient machines.
- Custom Solutions: There is a growing trend of producing customized blow-molded products to cater to niche markets, enhancing competitiveness.
Case Studies of Successful Companies
Several companies have thrived in the blow molding space due to their strategic decisions and innovative practices:
- Magic North America: By embracing Industry 4.0, Magic improved its production efficiency significantly while reducing costs and increasing customer satisfaction.
- Parker Plastics: Focusing on sustainable production practices, Parker has gained a competitive edge by using recycled materials in its blow molding processes.
Maintenance and Optimization for Blow Molding Machines
Preventative Maintenance Best Practices
Implementing a robust maintenance routine for blow molding machines can enhance performance and extend machine life. Key best practices include:
- Scheduled Inspections: Conduct regular inspections to identify wear and tear on parts before they lead to failures.
- Cleaning Procedures: Establish a regular cleaning schedule to remove residue and other contaminants that could impede performance.
- Lubrication: Maintain adequate lubrication of moving parts according to the manufacturer’s recommendations to prevent friction and wear.
Optimizing Production Efficiency
Maximizing production efficiency is essential for profitability. Strategies to consider include:
- Setting Optimal Parameters: Fine-tune machine settings based on material properties and desired output characteristics to minimize defects.
- Employee Training: Ensure operators are well-trained on the machine’s features and operational best practices to improve output quality.
- Utilizing Automation: Incorporate automation to handle repetitive tasks, thereby reducing human error and enhancing throughput.
Common Issues and Troubleshooting
Machine operators may encounter various challenges while using blow molding equipment. Common issues and their solutions include:
- Inconsistent Product Quality: Analyze machine parameters and material properties to identify root causes of defects, adjusting accordingly.
- Poor Cycle Times: Examine the entire production process; if slowing, it may indicate issues with equipment or operator efficiency.
- Frequent Downtime: Implement a robust preventive maintenance schedule to reduce unexpected machine failures and downtime.
The Future of Blow Molding Machines
Emerging Technologies in Blow Molding
As technology advances, blow molding continues to integrate innovations, leading to enhanced performance and sustainability:
- 3D Printing: This technology is beginning to play a role in product development, allowing rapid prototyping of blow-molded designs.
- Advanced Materials: The development of new lightweight and high-strength materials is shaping future blow molding applications.
- Smart Manufacturing: The incorporation of artificial intelligence will facilitate predictive maintenance and real-time monitoring of machine performance.
Sustainability Practices in Manufacturing
With the growing emphasis on sustainability, blow molding manufacturers are focusing on eco-friendly practices:
- Recycling Initiatives: Many operations are investing in recycling systems to reuse plastic materials, thus minimizing waste.
- Energy Recovery: Utilizing energy from production processes to power machinery is becoming increasingly commonplace.
- Green Materials: Manufacturers are exploring bioplastics and other sustainable materials to appeal to environmentally conscious consumers.
Predictions for Industry Growth
The blow molding industry appears poised for significant growth. Insights suggest potential developments will include:
- Increased Demand for Custom Solutions: Tailored blow-molded products will continue to become prevalent, especially in niche markets.
- Expansion into Emerging Markets: As manufacturing capabilities grow in developing regions, new opportunities are likely to arise.
- Technological Innovations: Advancements in automation and materials will shape product offerings and operational efficiency, further driving industry growth.
As the industry evolves, staying informed and adaptable is crucial. Engaging with reputable blow molding machine manufacturers can provide valuable insights into the latest technologies, trends, and best practices.