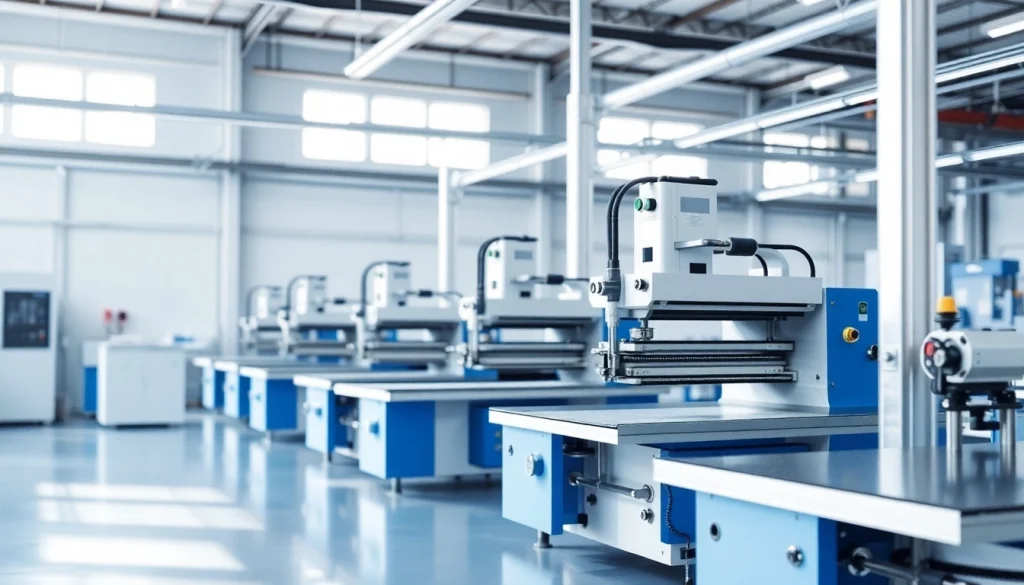
Understanding Precision Die Cutting
Precision die cutting is a manufacturing process that produces accurate shapes and designs by cutting through materials with high precision. Utilizing specialized tools and techniques, this method is commonly applied in various industries where exact replicas and consistent quality are critical. For more detailed specifics on this process, consider exploring precision die cutting techniques and capabilities. As technology advances, so do the methods and applications of die cutting, making it vital for companies to stay informed about industry trends and technical capabilities.
What is Precision Die Cutting?
Precision die cutting is a technique employed to create specific shapes from a wide variety of materials. This process ensures that each piece produced meets exact specifications, which is essential for industries that require high levels of accuracy in their manufacturing processes. The basic concept involves using a die, a specialized tool designed to cut through material, under defined conditions that render consistent and clean edges. The die can cut through materials ranging from paper, plastic, and rubber to metals, and it can produce intricate designs with unparalleled accuracy.
Key Features of Precision Die Cutting
The key features of precision die cutting that set it apart from other cutting methods include:
- Accuracy: Precision die cutting achieves tight tolerances, which can be as low as ±0.005 inches depending on the material and engineering requirements.
- Consistency: Once a die is created, it can produce thousands of identical pieces without variation, making it ideal for mass production.
- Variety of Materials: The technology can accommodate a vast range of materials, from soft foam to tough metals, providing versatility for various applications.
- Complexity: It can produce intricate designs, including complex contours and shapes that might be difficult or impossible to achieve with conventional cutting methods.
Common Applications Across Industries
Precision die cutting is utilized in numerous industries, including:
- Automotive: Used for components like gaskets, seals, and insulation materials.
- Medical: Critical in producing custom parts such as surgical instruments, medical device components, and disposable products with specific tolerances.
- Electronics: Important for crafting components like insulators, covers, and gaskets used in devices.
- Packaging: Utilized for creating specialized shipping and product packaging solutions that demand both protection and precision in design.
- Textiles: Applied in the fashion industry for cuttings in fabric pieces and other textile applications.
The Advantages of Precision Die Cutting
Cost-Effectiveness and Efficiency
One of the significant advantages of precision die cutting is its cost-effectiveness, particularly in high-volume production scenarios. After the initial investment in custom tooling, the cost per unit decreases with each additional piece produced. This efficiency in production is linked to:
- Reduced Waste: The precision involved with dies means minimal waste of raw materials, as each cut is made efficiently and effectively.
- Time Savings: The speed at which dies can operate allows for quicker turnarounds compared to manual cutting methods.
- Long-term Investment: Although the upfront costs for die creation can be high, in the long run, they pay off through cheaper production costs and reduced labor expenses.
Quality Control and Precision
Precision die cutting significantly enhances quality control in manufacturing processes. The inherent accuracy of this method allows for:
- Lower Tolerances: Manufacturers can define and achieve tighter tolerances that meet stringent quality standards.
- Consistent Output: Each die-cut piece remains uniform, ensuring that products meet functional and aesthetic requirements without discrepancies.
- Inspection and Adjustments: Implementing inline inspections during the die cutting process allows for real-time adjustments, further enhancing quality assurance.
Versatility of Materials and Shapes
The versatility offered by precision die cutting may be its most attractive feature. This technique can effectively handle an extensive range of materials, including but not limited to:
- Papers and cardboards
- Foams and rubber
- Plastics, including PET, PVC, and acrylics
- Thin metals and composites
This versatility allows manufacturers to experiment with various designs, styles, and functionalities, supporting diverse industry needs without sacrificing quality.
Types of Precision Die Cutting Techniques
Rotary Die Cutting Explained
Rotary die cutting is a streamlined technique commonly used for high-volume production. A cylindrical die rotates as it cuts through the material fed into it, offering several benefits:
- Speed: Rotary die cutting operates at high speeds, ideal for mass-producing simple cuts and shapes.
- Continuous Material Feed: This technique allows for continuous feeding of materials, leading to rapid production cycles.
- Lower Tooling Costs: While initial investments in rotary dies can be significant, they yield more pieces in less time, reducing overall production costs.
Flatbed Die Cutting Process
In contrast, flatbed die cutting employs a flat surface on which material is placed, and a press applies force through the die. This process offers distinct advantages:
- Complex Shapes: Flatbed die cutting excels in producing intricate designs that require more exact shapes, making it ideal for detailed work.
- Thicker Materials: This method is preferable for cutting thicker materials, as it accommodates more substantial substrates.
- Easy Setup: Flatbed processes can be set up without considerable machinery adjustments, suitable for prototyping and smaller runs.
Laser Cutting: An Emerging Technology
Laser cutting represents a modern alternative to traditional die cutting techniques. It utilizes a high-powered laser to cut through materials, providing remarkable precision and flexibility. Key attributes include:
- Intricate Detail: The focus of the laser allows for exceptionally fine details and patterns that might be difficult to achieve with conventional methods.
- No Physical Tooling Required: Unlike traditional methods, laser cutting requires no physical die, making it suitable for short runs and customized orders.
- Reduced Setup Time: Changes in designs can be executed quickly without the need for new tooling, significantly accelerating production processes.
Best Practices for Selecting a Precision Die Cutting Service
Evaluating Capability and Expertise
Selecting the right precision die cutting vendor involves careful consideration of their capabilities and expertise. Companies should consider the following:
- Experience: Look for providers with established records in your specific industry, as they will better understand the challenges and requirements.
- Technology: Invest in services utilizing the latest die cutting technology to ensure you receive the most efficient and precise results.
- Customization: Assess their ability to handle custom orders and flexibility in accommodating unique specifications and designs.
Understanding Tolerances and Quality Standards
Understanding the tolerances that your project requires is crucial. Different projects may demand varying levels of precision, and it’s essential to communicate these needs specific to your piece. The tolerances for die cutting generally range from ±0.005 to ±0.01 inches; however, advanced laser cutting techniques can achieve even finer tolerances. Ensure that your selected service adheres to relevant industry quality standards, such as ISO certification, that align with your expectations.
Getting Quotes and Comparing Services
Once you’ve narrowed down potential die cutting vendors, gathering detailed quotes is the next logical step. Consider the following:
- Transparent Pricing: Ensure that all costs are broken down, including setup fees, material costs, and any potential tooling expenses.
- Lead Times: Compare production timelines and ask about any guarantees or rush services if necessary.
- Samples and Prototypes: Request samples of previous work to gauge their finished product quality and precision.
Future Trends in Precision Die Cutting
Advancements in Technology
The die cutting industry is rapidly evolving due to technological advancements. Innovations such as automation, robotics, and smarter software solutions are transforming traditional methods, resulting in increased efficiency and productivity. As these technologies mature, we can expect higher levels of customization and even more precise cutting capabilities.
Impact of Industry 4.0 on Die Cutting
As part of the Industry 4.0 trend, precision die cutting is increasingly integrating IoT (Internet of Things) capabilities. Machines can now exchange data to optimize processes, predict maintenance needs, and streamline operations. This interconnectedness allows companies to minimize downtime and enhance overall efficiency in their production lines.
Sustainability in Precision Die Cutting Processes
With sustainability becoming a critical concern across industries, precision die cutting is no exception. Manufacturers are adopting greener practices by utilizing eco-friendly materials, reducing waste, and implementing energy-efficient processes. Companies that prioritize sustainability not only contribute positively to the environment but may also see improved customer loyalty as consumers increasingly prefer eco-conscious brands.